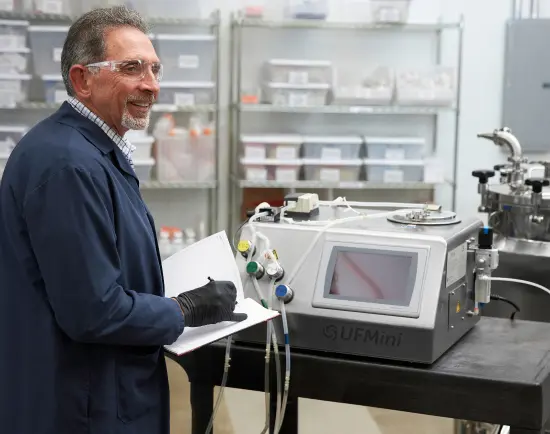
Our purpose-designed state-of-the art cell separation solutions meet the specific needs of a variety of applications, from Cell Therapies to Cellular Agriculture.
Streamline your cell therapy development and manufacturing with a scalable, low-shear platform designed to maintain cell viability. UniFuge® offers capabilities beyond cell harvesting, supporting gene editing, cryopreservation, and bioreactor expansion for consistent results from research through large-scale production.
Increase product yield, reduce downstream impurities and cut production costs with the UniFuge® platform. Optimize lentiviral and AAV vector production with low-shear technology for cell separation and overcome titer loss, filter clogging, and contamination in shear-sensitive applications.
Accelerate mAbs and other biologics development with UniFuge®. Our low-shear centrifuge supports critical processes, including seed banking, cell retention and clarification, enabling process intensification and supporting high product yield and purity throughout development and manufacturing scale-up or scale-out.
Optimize cell agriculture workflows with versatile, gentle cell handling for consistent scalability and efficiency. Achieve high viability and tunable processing from lab to full-scale production with the UniFuge® single-use platform and ViaFuge® for SIP/CIP applications.
Enhance vaccine production with UniFuge®, ViaFuge®, and PowerFuge®. These centrifuges are designed for reliable, scalable vaccine development, offering flexibility for both live virus and recombinant vaccines.
Achieve high-yield plasmid DNA production with low-shear centrifuge technology designed for efficient harvesting and clarification. UniFuge®, ViaFuge®, and PowerFuge® support scalable workflows from research to large-scale manufacturing.
Streamline microbial fermentation workflows with high-performance centrifuge solutions designed for diverse applications. PowerFuge®, UniFuge®, and ViaFuge® deliver scalable, efficient separations for both intracellular and extracellular products.
Our wide range of separation solutions enable robust scale-up and scale-down and facilitate the transfer of operating protocols from early-stage development to commercial manufacturing and licensure.
Get in touch with a sales representative, request support or download our free white paper.
Contact Us